GRUPPO TRINITA’ INDUSTRIA SALUMI: Industry 4.0 in a food company
2025
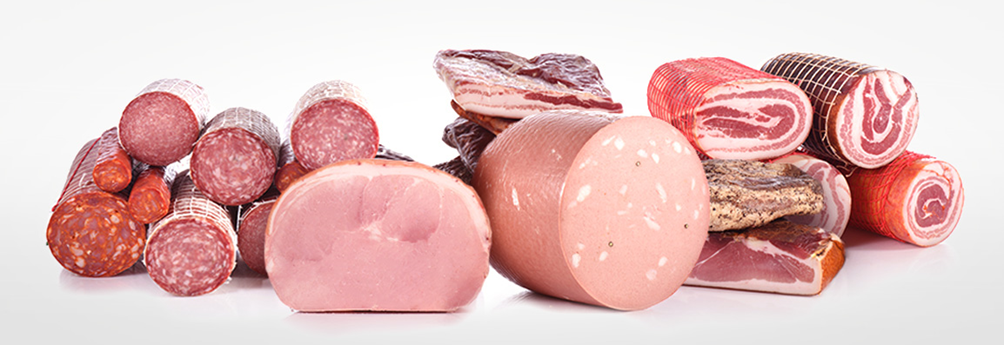
THE CHALLENGE
Trinity was founded in 1982 in Buttapietra, in the province of Verona (Italy), by three entrepreneurs specializing in pork processing. In 1994, the company built its current headquarters in Vallese di Oppeano, and in the following years it expanded rapidly, acquiring other companies in Italy and becoming a full-fledged Group.
Today, the Trinity Group consists of six Companies certified to standards such as BRC, IFS, FSCC 22000 to ensure quality and safety.
The Group offers a wide range of delicatessen products, including hams, mortadella, coppe, pancetta and salami, also available in take-away formats to meet the convenience needs of modern consumers.
Trinity’s ambition has led the company to optimize its production processes. For this reason, from 2022 it chooses together with Orchestra to upgrade its fleet by digitizing as many as 21 machines. A choice that allows the company to automate the management and monitoring of production orders while taking advantage of the tax benefits provided by the Italian Transition Plan 4.0.
THE SOLUTION
At Trinity, Orchestra installs RETUNER®, the new digital solution designed to help companies plan, monitor and manage machine operations in production.
This solution includes MES software, developed specifically for SMEs in the food sector, to make the entire production more efficient and controlled.
THE BENEFITS
The introduction of RETUNER® in the company has brought a number of benefits, including:
- Ability to access Industry 4.0 financing
- Opportunity to be able to overhaul production layouts
- Opportunity to access production data hitherto unavailable based on which to define performance indicators (kpi)
- Opportunity to obtain objective data for evaluating productivity
“The modular structure makes the software adaptable to business reality”, says Stefano Zattoni, Quality Manager at Trinity today.